HDPE Line Replacement Project Management For Hampton Roads Sanitation District Plant Decommissioning Project
Learn why the Hampton Roads Sanitation District partnered with Ferguson Waterworks for HDPE Line Replacement Project Management and supply solutions during their plant decommission project that required replacement of a 9,000 ft sewer main.
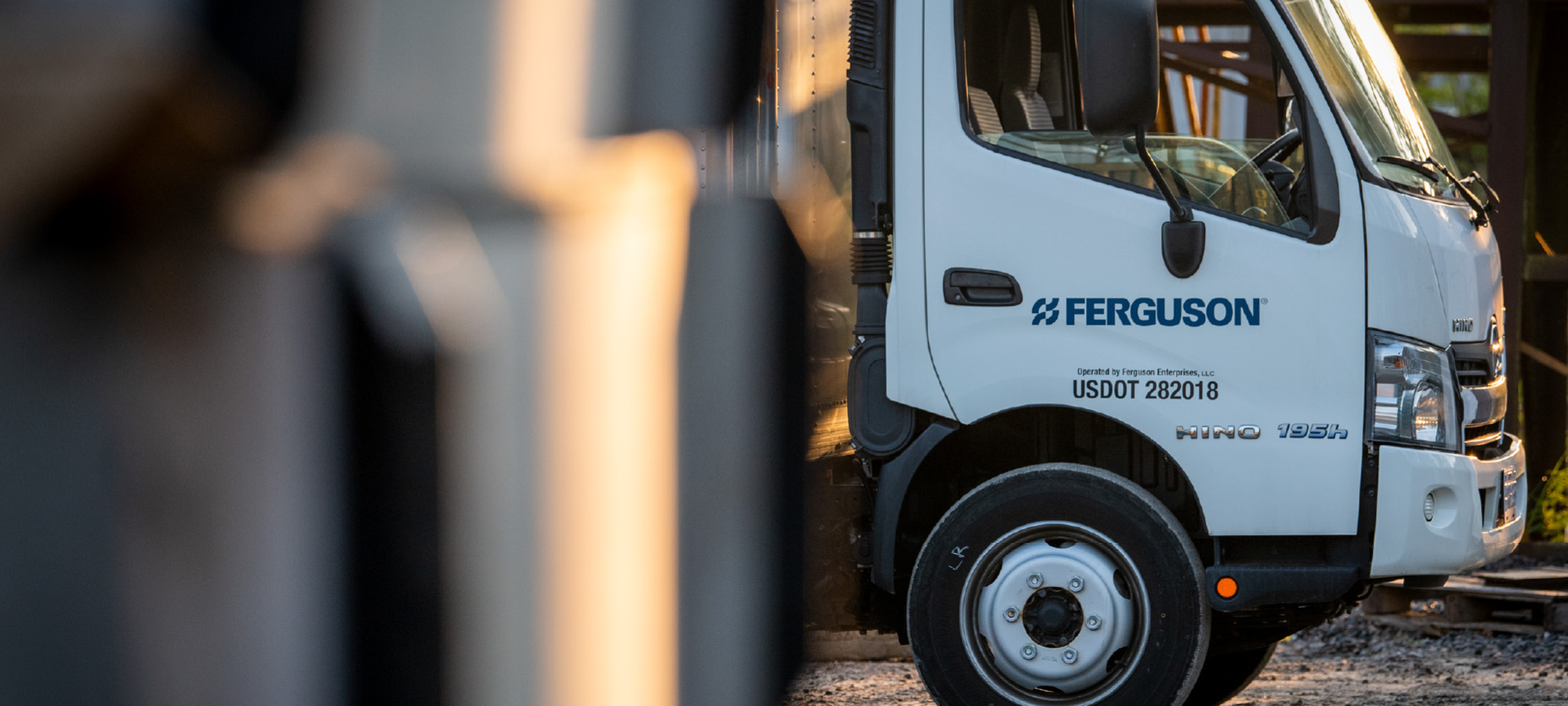
Background
The Hampton Roads Sanitation District is one of the largest wastewater treatment organizations on the East Coast, managing wastewater from the North Carolina line to Virginia’s Northern Neck region. A plant decommissioning required a flow redirect and replacement of 9,000 feet of 24-inch sewer force main that had been in place since the 1950s. To meet the minimum requirements for the new use, the sanitation district needed 7,000 feet of 42-inch ductile iron and 2,000 feet of 48-inch high-density polyethylene pipe.
The project was complicated by two facts. First, the line ran down the middle of Virginia Beach Boulevard, a heavily traveled and often-congested six-lane road. Second, the line was flanked by a sensitive wetlands area. The installation necessitated five tunnels underground and submergence in salt water.
Recommendations & Installation
When Bridgeman became the project’s senior manager, he turned to Ferguson Waterworks, a trusted partner with a strong success record. He said the company assisted in multiple ways, including:
Careful project management:
Completing a project of this scale and in a complicated location requires strong project planning and execution. Ferguson Waterworks will “read the spec, and if something doesn’t look right there, they’ll email the owner to ask questions and to make corrections,” Bridgeman said. “Ferguson was able to work with the ductile supplier and move stuff around on the schedule.”
Expert consultation:
The original project was designed with mechanical joint fittings where the pipe came out of the end of the tunnel: An HDPE MJ adapter to an MJ 90 that rose vertically 30 feet, to another MJ fitting to reach at least a 12-foot elevation. This took place at the job site. “What happens if one of those fittings ever leaks down the road due to stretching, age, or whatever?” Bridgeman wondered. “When you’re deeper than that, who knows years from now how much it could cost you to get back down to that fitting.”
Ferguson Waterworks suggested transitioning over to a fully fused HDPE to avoid a deeply buried mechanical connection and possible leakage.
Environmental sensitivity:
To safeguard the surrounding wetlands and creeks, the engineers relied on a bentonite fluid — an environmentally friendly silica clay — to carry the soil back to the boring machine.
“No fish, no anything, were impacted,” Bridgeman said.
Advanced technology:
Using electrofusion to couple the riser to the pipe allowed the team to minimize the amount of equipment it used, said Rob Naquin, a Ferguson Waterworks outside sales representative.
“When you have a pit that’s 65 feet, every foot bigger is more liability, more money. Just more problems, more de-watering and all that,” Naquin said.
Because the crew didn’t need heavy machinery in the tunnel or pit, potential impacts to the environment and traffic flow were reduced, liability and costs were lowered, and potential associated problems and dewatering were averted. The 48-inch electrofusion couplings were fabricated at one of Ferguson Waterworks’ ISO-certified pipe fusion facilities and brought on-site.
“Ferguson is really the only one that specializes in HDPE, as well as the ductile and the valves and everything combined,” Bridgeman said. “Other vendors can sell you the HDPE, but they’re not fabricators. And their guy can be on a truck and here tomorrow. That did make it attractive for me to work with Ferguson.”
Additionally, Bridgeman had all his fusion techs trained by Ferguson Waterworks to make sure his team was up to speed on this state-of-the-art technology. Ferguson Waterworks data logged every component to provide testing reporting on the integrity of the process and verify that all the welds were done following associated ASTM standards.
The final installation consisted of eight pits — 45 feet long, 20 feet wide, and 45 feet deep — and two tunnels. After pouring a concrete slab, the team installed a 60-inch diameter steel casing 46 feet deep from one side of the London Bridge Creek to the other and ran the HDPE through the tunnels with spacers to align them in the center.
The Results
The project was originally estimated to take two years, but it was completed in just six months. Wastewater has successfully been redirected away from the decommissioned plant, and the Virginia sanitation district’s new HDPE pipes should last, undisturbed, for years.
“It’s just a better pipeline now that won’t break and have massive sewage spills. It’s a bulletproof system,” said Naquin, who sees more projects like this one on the horizon. To update dated systems and to address rising sea levels, “there’s a lot more complicated work like this coming out,” Naquin said. “Everything’s moving that way.”
Working with a trusted partner was critical, Bridgeman said.
“Having done hundreds of projects with Ferguson and buying hundreds and hundreds of thousands of feet of HDPE from them, I was very confident going into this,” Bridgeman said. Working with Ferguson Waterworks also lessened the timetable.
“The fact that Ferguson was able to supply every piece of the project as a manufacturer, as a distributor. To get me every piece of this project from one person instead of having to deal with 10, it always adds to the value of the project.”
View Similiar Case Studies
In order to revitalize and meet stormwater codes, the abandoned parking area at the Shoppes at Fashion Square in Orlando, FL, required updates. With a permeable paving system and machine technology, we helped the client achieve their goals, save $1 million, and complete the project in just 10 days.
With solar panels in place and operational, an immediate and effective erosion control solution was imperative. Especially considering the panels were positioned next to channels, drip lines, and spillways.
After failed attempts to stabilize the earth at the Mt. Jackson Solar Farm, they required an immediate, cost-effective erosion control solution. Ferguson Waterworks was brought on board to address their ongoing concerns.